GUM BLANKETS AND THE CIVIL WAR
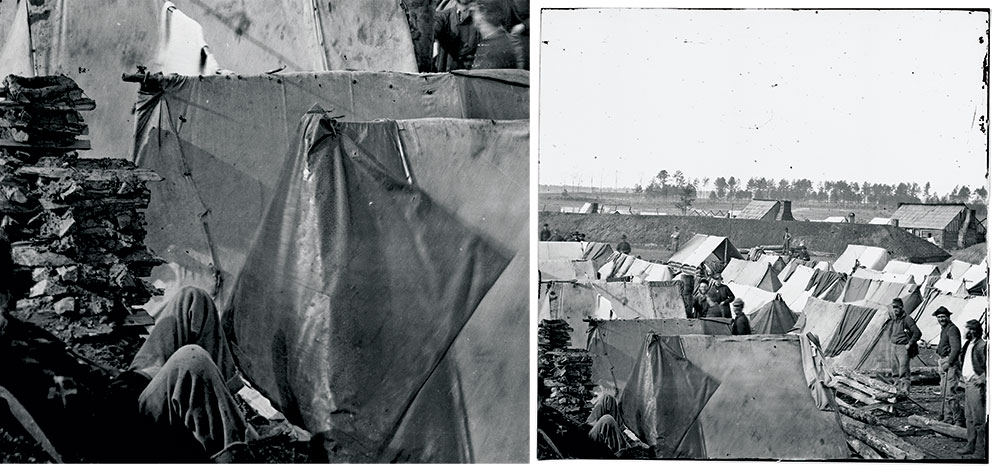
View of the Forth Burnham encampment and earthworks showing a
rubber blanket used to close the end of a canvas tent. Library of Congress.
If you have ever gone camping, you have probably placed a plastic tarp under your tent, to keep moisture away from your tent and your bedding. Civil War soldiers left their homes for camping trips which went on for years. Plastic tarps didn’t yet exist, but most Union soldiers had a rubber blanket, sometimes called a gum blanket, or a poncho with a slit to allow it to be worn over the body in wet weather. Soldiers could use the rubber blankets as ground cloths, or several soldiers could work together to turn rubber blankets into a tent, or just put one over the entrance to the tent as in the picture above.
Why is this showing up in a story about the Deserted Village of Feltville? First, because Warren Ackerman—who you may recall bought the village at auction—built a fortune based largely on rubber blankets sold to the Union Army. Warren’s biography in F. W. Ricord’s History of Union County, New Jersey indicates that the several rubber companies Warren came to own “supplied the United States government with a large portion of its best rubber goods.” 1 Mike Woshner’s book, India-Rubber and GuttaPercha In the Civil War Era, shows that Warren’s contracts to supply goods, including rubber blankets, began in 1862.
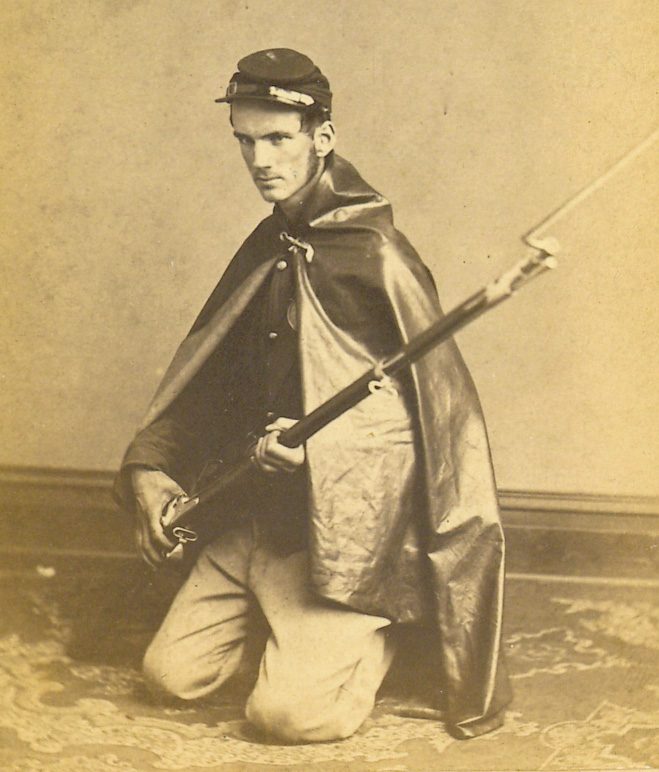
Carte de visite by Robert W. Addis of Washington, D.C. showing an infantryman wearing a rubber blanket around his body.
Ronn Palm Museum of Civil War Images Gettysburg, PA.
But why do I care about Warren’s rubber blankets? Because it turns out they were one of the thing which a soldier could use to reduce the chance that he would die of disease or exposure as he faced the poor food, muddy marching, and temperature highs and lows of an extended camping trip fighting to free the slaves and bring the South back into the United States.
Why also do I care about Warren’s rubber blankets? Because in making rubber blankets and other rubber goods, he became part of a contentious and often ruthless industry, that was still struggling to make items that wouldn’t disintegrate during use. I think of this as the time of the rubber wars. Warren was definitely a player.
DEATH IN THE CIVIL WAR
It is estimated that about one quarter of the soldiers who marched off to battle in the Civil War never returned home. One estimate, from the American Battlefield Trust puts the number of deaths to be at least 620,000, 2 and another Civil War scholar, Dr. Bonnie Brice Dorwart, puts the estimate at a whopping 700,000.3 Whatever the number, the deaths amount to more than all the casualties in the First World War and the Second World War combined.4
The American Battlefield Trust indicates that disease killed twice as many soldiers as battle did, while Dr. Dorwart says that disease killed more than 400,000 soldiers of her 700,000 estimated deaths. Both sources agree that this was due, in part, to the state of medicine at the time and the lack of adequate medical supplies, which greatly increased the amount of deaths which should have been avoidable.5 While clearly some of these potentially avoidable deaths followed treatment for battlefield wounds, many deaths were the result of conditions soldiers developed during the close quarters and difficult living conditions that the soldiers faced day to day.
Indeed, there was a long list of diseases which could incapacitate or kill a Civil War soldier. Dysentery was perhaps the most prominent, but the list includes typhoid fever (spread by lice), malaria, pneumonia, smallpox, and yellow fever, just to name a few. Disease was spread far too easily in camp and on the march, where soldiers spent most of their time, the time in battle being a small part of the experience of going away to a war.
Common factors in the spread of disease were lack of hygiene, spoiled food, contaminated water, and lack of access to doctors and surgeons. Typically cooking pots might also be used to boil lice infested clothing and latrines were dangerously close to water sources. But all sources agree that exposure to the elements was a significant contributor to deaths in the war.
As I searched for primary material on Civil War conditions and the use of rubber blankets, I found an amazing book—it seems like I find one every month—that begged to be read in its entirety. This month, it was a book called Gone for A Soldier: The Civil War Memoirs of Private Alfred Bellard. Private Alfred Bellard was a soldier from my home state of New Jersey (but a transplant from England). Bellard volunteered for a three-year enlistment in the Union Army from his home of Hudson City, New Jersey, which is now a part of Jersey City, New Jersey. Bellard served from 1861 to 1864 with Company G, Fifth Regiment, N.J. Volunteers. While serving, he wrote a journal and extensive letters, which he later edited, detailing day to day life as a soldier. He also made amazing drawings, many in color, to go with the letter and journal entries. I don’t know how to get permission to use any of those, so I will direct you to the book (I’d love to be responsible for a run on the book from libraries and book dealers). Bellard wanted to both give those at home a sense of what was going on, and also have something he could go back to later to remind him of his experiences.
Bellard apparently had no intention of publishing his material, and the collection of letters and journals was discovered by something of an accident. Indeed, the man asked by a publisher to edit the papers into book form, Civil War expert David Herbert took his time authenticating everything first. He describes himself as initially suspicious of such an amazing cache of recollections. Herbert added explanatory notes at the beginning of each of his edited chapters.
Bellard gives a detailed picture of what each battle was like, including often gruesome descriptions of the dead and wounded. He also gives a window into camp life—including the accommodations created by soldiers on the march, and their food (including constant descriptions of raiding nearby farms and other creative ways of supplementing their daily diet).
I mentioned bad food, and cooking pots used to boil clothing clean. Bellard includes one especially detailed description of the food and the multiple uses of the cooking pots. It illustrates some of the less than healthy conditions faced by the Union soldiers, and the fact that soldiers had to use their own funds to supplement rations:
The raisons [sic] mentioned, were bought out of the company funds and had nothing to do with Uncle Sam. The desacated [sic] vegetables were all kinds of green stuf [sic] pressed into a square cake, and when we wanted any soup a piece of it was broken off and put in the pot, when it would swell out and make a very nice soup. The bean soup was good, but with some cooks it was made so thin that the boys used to say that there was one bean to a quart of water. Our coffee when we first went out was issued to us green, so that we had to roast and grind it, which was not always a success, some if it being burnt, whale some would be almost green. In roasting it we put a quantity of it in a mess pan, and placing the pan over the fire would have to keep stirring it round with a stick in order to have it roasted as evenly as possible.
These mess pans were used to fry our pork in and also as a wash bason [sic]. Our soup, coffee and meat were boiled in camp kettles suspended over the fire . . . which were also used for boiling our dirty clothes. Not a very nice thing for a soup pot, especially when they were full of vermin, as they were most of the time when on active service. Our stomachs were strong enough however to stand it, and our appetites did not suffer on that account.
Fresh beef was taken along with us on the march, the cattle following in the rear of the army to be killed when wanted. When the quartermaster wanted some fresh beef, some of the men who were good shots would go with the butchers to the drove, and having selected the oxen, a ball would be fired into his head, and as soon as he was down, his throat was cut by the butcher, after which the carcas [sic] was cut up and issued to the companys [sic]. On one of the hot days at Fair Oaks, the meat when issued to us was fly blown, and the maggots had to be scraped off before it was put into the pot, although the beef was just killed and was yet warm when I carried some of it to the cooks. The salt junk as we called our pork was sometimes alive with worms, as was also an occasional box of crackers, but that did not happen very often.6
Bellard’s account carries nearly constant descriptions of pilfering and looting for food and other supplies from both local farms and homes, and even stealing from stores and “sutlers,” the latter being vendors who followed the army to sell supplies to soldiers, at prices they considered extremely exorbitant, thus justifying the occasional theft. Initially, and later, intermittently, officers tried to enforce a policy against such acts, but as the war went on, officers even concealed thefts which they knew of, when faced with irate local residents who had suffered a loss.
Bellard’s memoir contains graphic descriptions of battlefield wounds and death, hospital treatment (noting in at least one location a box under the operating table where there was a pile of amputated limbs). He also describes marching through mud so thick it was hard to keep shoes on and getting thoroughly drenched and/or chilled during marches or camp life. Sometimes the soldiers had time to construct structures or tents, sometimes they slept out in the open. Bellard also describes constant desertions, although he never considers desertion, exhibiting considerable equanimity in the face of trying conditions.
Dr. Dorwart indicates that the lack of sanitation often found in Civil War camps was not due to a lack of knowledge about the importance of sanitation; for support, she cites to the “sanitary reform movement” which had evolved between 1800 and 1860, including a major report in 1850, Report of the Sanitary Commission of Massachusetts, 1850, by Lemuel Shattuck, Sanitary Commission: London School of Hygiene and Tropical Medicine. She notes that journals of the surgeons (as all doctors were referred to) serving in Civil War hospitals, both temporary or more permanent, contained constant references to disease being everywhere.
Dr. Dorwart suggests that a lack of discipline coupled with the sheer overload of daily tasks were reasons for poor sanitation. Apparently, adding to a somewhat cavalier attitude toward sanitation, including the need for prompt burying of soldiers and dead horses, prompt attention to the feces of both horses and people—including latrines dug to the proper depth and at an adequate distance from the camp. This cavalier approach was partly due to the fact that observers had noted that illness rates were often the same regardless of precautions. Bellard’s company, at least, got recognition for maintaining clean and neat camps. On the other hand, he also comments on at least one occasion about how long it has been since either he or his clothing has been washed. The water his company found for drinking and washing was often muddy or otherwise contaminated.
When Bellard finally does receive a battlefield wound that renders him unable to fight, he first tries to treat it himself, fearing that he will become one of the soldiers whose leg is in a box under the table.
GUM BLANKETS
I envision the pilfering and looting for food that Bellard and his compatriots as an example of how the soldiers tried to improve their conditions while they were serving. The rubber blankets they carried, largely issued by the government, were another especially dramatic way of improving conditions.
Woshner’s book India-Rubber and Gutta-Percha In the Civil War Era, indicates that, long before rubber blankets became a crucial element in the Civil War, a Boston man, James Boyd, had written to the War Department in 1836, saying:
I forgot to mention to you in conversation that in Washington the idea was suggested of using some of my India Rubber goods as a kind of sheet to spread under the men in their tent. These would effectively prevent the damp of the ground from striking on the men and might be made so that each man would have one or, one might be made large enough for each tent. By the former method, it might be used round the shoulders when on the march in rainy weather and a s sheet at night.7
Lawrence Babits, in his article “Rubber Poncho and Blankets from the Union Transport Maple Leaf” calls these “crucial items in the Civil War soldier’s equipage,” and notes that issuance of these blankets was ordered by the Secretary of War as of November 1861.8 Unfortunately, rubber blankets, and other rubberized items, including shoes, from the Civil War have generally not survived down the years, with their importance thus literally rotting into obscurity.9
As noted, today we would think of these blankets as a type of tarpaulin, which are now made of plastic to keep moisture from wicking through. In the mid-nineteenth century, plastic was many decades away, and rubber, the top-of-the-line material for these blankets, was just out of its infancy, having been improved by careful work in various parts of the world so that it would not become brittle at below freezing temperatures or begin to melt and get sticky at higher temperatures.10 More on those developments will be found below.
The waterproof blankets issued during the Civil War generally had a cloth substrate layer, often cotton duck or muslin, which was then coated on one side with a waterproofing agent.11 While some of these blankets may have been made with varnish, most were rubberized. Manufacturers of rubber blankets began by rubberizing both sides but soon switched to rubberizing only one side of the blanket. This both kept costs of manufacturing the blankets down and reduced the weight of items carried by soldiers as they marched from camp to camp or battle to battle, a factor that sometimes meant life or death.12
Historian Frederick C. Gaede credits Major General George B. McClellan as being one of the early promoters of waterproof items for the comfort of soldiers under his command, after having observed various such items provided to French soldiers in Crimea.13 Quartermaster General Capt. Montgomery C. Meigs, acting on orders to procure waterproof blankets, initially instructed that the blankets issued to soldiers were not to exceed 2 ½ pounds in weight; later in the war they weighed 2 ½ to three pounds.14 There were two variations on the rubber blanket—ponchos, which had a reinforced slit, so they could be put over the head, and more simple rubber blanket without the slit.15
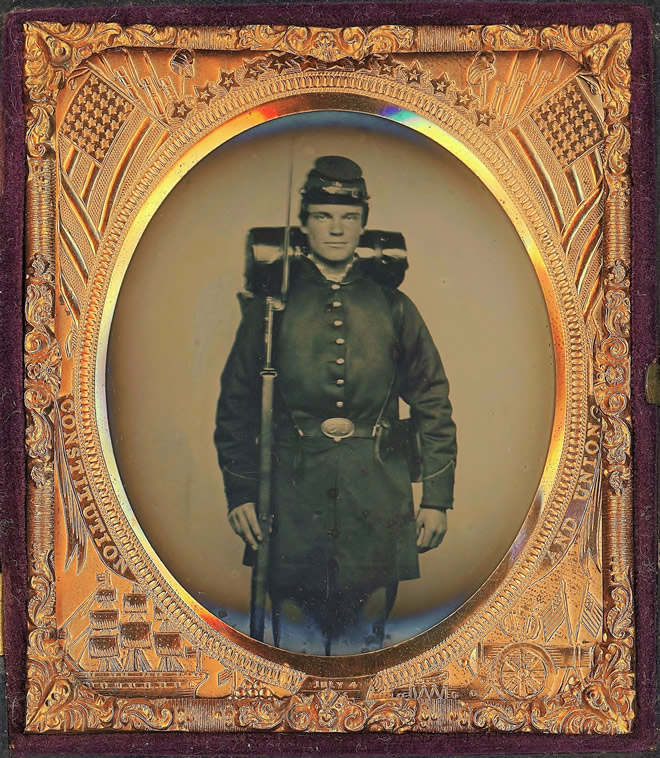
Photo showing an infantryman with his rubber blanket wrapped around a wool blanket, keeping it clean and dry.
Sixth plate ambrotype by an unidentified photographer. Dan Binder Collection.
Soldiers were quick to recognize the value of rubber blankets. Historian Lauren McGowan’s research suggested that soldiers would frequently abandon their heavy knapsacks, shedding unnecessary weight, and carrying only a bed roll which consisted of their rubberized blanket and perhaps a wool one rolled around what few personal and valuable items they could not bear to be parted from.16 Bellard describes multiple times when the knapsacks were sent with a pack train, and the soldiers carried only their bedroll and a few other items for easier movement of troops.
One soldier described his feelings about his gum blanket thus (the frequent misspellings are in the original):
[I]t’s mighty good ter spread on the ground under yer blanket when ye goes ter bed. Ye know wet won’t soak through Injy-rubber, ‘n’ it’ll help pervent ye ketchin’ the rumaticks. ‘Sides that, when ye have ter lie down ‘n the mud it keeps yer blanket clean. Then when ye’re marchin’ in the rain it beats ‘n umbreller all holler.17
The issuance of a rubber blanket to a Union soldier was even used as a recruiting inducement.18 One regiment in Philadelphia was particularly aggressive in using gum blankets as an inducement to voluntary enlistment, with what seems to be an entire column of classified ads on October, 27, 1862—one day ahead of an imminent draft–all promising benefits to any would be soldier who immediately joined the 157th Regiment. Each ad is slightly different, and all are a call to action. I have included the text of three of my favorites:
AVOID THE DRAFT.—JOIN THE
One-hundred-and-fifty-seventh Regiment, Col. WM. A. GRAY.
Complete outfit, one month’s pay in advance, all the
bounties and a gum blanket.
Call at No. 627 Chestnut street.
PHILADELPHIA CITY GUARD,
One-hundred-and-fifty-seventh Regiment P. V.—Phila-
delphians, awake! If you would avoid the Draft on the 28th,
enlist or send recruits to the One-hundred-and-fifty-
seventh Regiment. One effort on your part, and the work
is done. All the bounties, one month’s pay in advance,
and a Gum Blanket to each man.
PHILADELPHIA CITY GUARD.—PHILADELPHIA CITY GUARD,
Enlist in this Regiment and secure all the Bounties and a
Gum Blanket. Drafted men get no Bounties, and have to
furnish their own blankets. Call before it is too late.
Head-quarters. No. 62 CHESTNUT street.19
Bellard includes a description of one way the soldiers used their gum blankets to keep warm and dry on a particularly cold night, when tents could not be erected:
After [the fire] had got into a good blaze, the beds were made. Our rubber blankets were placed on the ground to keep out the dampness (in a circle round the fire) with some of the woolen blankets over them to keep us warmer. We then lay down spoon fashion, with our feet to the fire, and after covering ourselves with the balance of the rubber and woolen blankets where [sic] fixed for the night. Although it was a terrible cold night, we slept very comfortable. The only trouble with the spoon fashion of sleeping being that when one man wanted to turn over, all the rest had to turn with him, or else loose [sic] our covering.20
McGowan indicates that, since the Confederate Army generally provided a much inferior canvas blanket coated only with linseed oil, Confederate soldiers routinely stole Union soldier’s rubber blankets from dead or captured Union soldiers.21 There is a description of rubber blankets being used by Confederate soldiers turning in for the night, in Detailed Minutiae of Soldier Life in the Army of Northern Virginia, 1861-1865, published in 1882 by Carlton McCarthy, identified as “Private Second Company Richmond Howitzers, Cutshaw’s Battalion Artillery, Second Corps, A.N.V.:”
But now, there they go, one by one; no, two by two. Down goes an old rubber blanket, and then a good, thick, woolen one, probably with a big “U.S.” in the centre of it. Down go two men. They are hidden under another of the “U.S.” blankets. They are resting their heads on their old battered haversacks. They love each other to the death, those men, and sleep there, like little children, locked in close embrace.22
The emphasis in this passage on the “big U.S.” on the woolen blankets made me wonder if the author was suggesting that the blankets this group had were pilfered from the Union Army.
GUM BLANKETS AND THE GREAT RUBBER WARS
James Boyd may have suggested that he could supply rubber sheeting to help soldiers keep out the damp in 1836, but he was speaking from a time when rubber was very much not ready for prime time. Rubber’s history goes back to use by indigenous people for centuries, before the first colonial efforts to the New World. Columbus is credited as the first European to record an observation of natives using rubber, sometime between 1493 and 1496.23 Rubber products of many kinds, including rubber balls, were being used by indigenous people across Central and South America. The product became known as “India Rubber,” because it came from what Europeans were calling the Indies.24
Starting in the first half of the nineteenth century, entrepreneurs and companies big and small were racing each other to produce usable rubber products. Although there were a few different raw materials being explored for use, this discussion will focus around the India-Rubber made from Caoutchouc, a latex or gum produced by an Amazon region tree. Early manufactured rubber products would melt or become soft and sticky in hot conditions; after an hour or so in the sun, the surface would break down and start to smell.25 In cold weather, items would become brittle and equally unusable as in warm conditions.
Various individuals tried to improve rubber’s performance with the application of various materials. Charles Goodyear was one of these individuals, pursuing every lead and trying every option, driving his family into poverty in his obsession over rubber, which he had somehow fixed on being the way he would make a fortune.26 Along the way, Goodyear turned to Nathaniel Hayward, who had discovered that sulphur could be used to improve make rubber more usable. Goodyear began to work with Hayward and offered to help the illiterate Hayward procure a patent in both men’s names. The two men reached an agreement which allowed Goodyear to take over ownership of the resulting patent upon a final payment—which Goodyear was hard pressed to come up with. Hayward would be allowed to make rubber products until the patent became solely Goodyear’s.
At the last minute, Goodyear convinced Hayward that Goodyear needed to take the patent out under his own name, without recognition to Hayward. Hayward reluctantly agreed, provided the other agreements between the parties were fulfilled, but for the rest of his life, felt he had been ill-treated.
Truthfully, Hayward’s use of sulfur had only taken the resulting product so far, and it needed further work on Goodyear’s part to fully eradicate the problems rubber products experienced during use in warm and cold weather. Goodyear worked tirelessly, and eventually perfected a process which applied sulfur to rubber at between 250 and 280 degrees Fahrenheit. English inventor Thomas Hancock developed a similar process, for which he received an English patent soon after Goodyear’s American one. It is Hancock’s friend “a Mr. Brockedon”28 who is credited with naming the process in general calling it “vulcanization,” after the Roman God Vulcan.
Vulcanization made resulting rubber products more supple and durable in all conditions. Babits explains that “Chemically, vulcanization is the cross-linking of isoprene chains by Sulphur, which results in a strong, elastic three-dimensional network.” 27 The resulting rubber could not only remain stable in various temperatures but would resist impacts by oils or turpentine. The rubber was also non-adhesive. Goodyear’s process received an American patent in 1844.
Goodyear began selling licenses under his patent to various companies. Around 1844, Goodyear sold an exclusive license to a man named Daniel Suydam to use his process—and patent—in the creation of shirred rubber products.29 Shirred rubber products were an interweaving of rubber threads into cotton or some other non-rubber fabric, with the rubber threads being stretched during the application process. At rest, the rubber would return to its non-stretched length, making the fabric pucker, and still be stretchy. Goodyear’s first application of this fabric was in men’s suspenders, which became popular, since men could appreciate the elastic nature of the suspenders, and soon grew to appreciate the puckered appearance.30
My last post mentioned Horace Day, who had been one of the first to start manufacturing rubber goods in New Brunswick, losing his factory there as a result of being found guilty of Goodyear patent violations. Indeed, Horace Day, having received no Goodyear license, began making the exact type of products for which the license had been issued to Suydam. Goodyear brought litigation against Day, on behalf of himself and Suydam, but the latter became so infuriated during the course of the litigation, that he dropped out of his shirred goods agreement. In the settlement which resulted, Day acknowledged Goodyear’s patents, and Goodyear allowed him to take the exclusive shirred goods license, for a lump sum payment and an agreement to pay royalties to Goodyear of 3 cents per yard of shirred material Day made. Goodyear even subsequently made efforts to drive any would-be competitors out of the shirred rubber market.
By this time, eight or nine companies had licenses from Goodyear to make rubber products of various kinds, other than shirred goods. Day almost immediately began to manufacture products not covered by his license, and also failed to pay the royalties agreed for the shirred products. Day began claiming that the products he manufactured were made using processes created by individuals other than Goodyear, including Hayward, who was still disgruntled over his treatment by Goodyear; Day stamped items with the inscription “N. Hayward, Inventor of the Improved Gum.”31
The matter came to a head in “The Great India Rubber Case,” in which Goodyear once again sued Day over patent violations. By this time various of Goodyear’s licensees had bonded together, some starting an organization originally based around the manufacture of rubber shoes, called the Goodyear Associates and Licensees.32 The Newark India Rubber Company—the company where Warren began his rubber career—was one of the companies in this group. The group renegotiated their payments to Goodyear, making their per item cost significantly lower. After doing so, the group immediately sold a sub-license to two other companies, charging a higher price per pair of shoes. This gave the group income, which was apparently used by them and Goodyear to hire one of the country’s then most famous attorneys, Daniel Webster. The case seems to be rather celebrated—Ricord explains that it was the last “great forensic effort of [Daniel Webster] eminent American statesman and jurist.33 The court was unimpressed with Day’s attempts to downplay the validity of Goodyear’s patent and of his years of work and rejected arguments that many people had discovered ways of improving rubber, and that Day’s manufacture of items other than shirred goods was somehow valid under his own rubber discoveries or those of someone else other than Goodyear. The court issued a “permanent injunction” against Day manufacturing rubber goods, and referred the case to a court-appointed master for determination of what damages should be.
The whole history gets even more weird and sticky at this point. In spite of the original “permanent injunction” against Horace Day engaging in the rubber business, no less than the United States Army turned to Day in 1861 to supply rubber tents, called Poncho Tents, to the army. It is not clear what had happened in between to allow Day to regain his footing in the India Rubber business.
WARREN ACKERMAN’S COMPANIES AND UNION ARMY CONTRACTS
As noted, Ricord indicates that Warren Ackerman’s companies supplied the Union Army with a substantial amount of the rubber goods to outfit its soldiers. Woshner’s book identifies rubber blankets as chief among the goods supplied by Warren’s companies.
Indeed, even before the war, in 1847, the Newark India Rubber Company, Warren’s first rubber company was advertising its line of products allowing one to “Prepare for Wet Weather.”34 The advertisement first mentions rubber shoes, under the Goodyear patent, and then notes “Every description of air tight and water-proof goods in use, wholesale and retail.” In 1848, the company advertised a long list of rubber goods, including “250 pieces of India Rubber Carriage Cloth. 200 India Rubber Coats and Cloaks.”35 In 1849, the list advertised was even longer, and included “Carriage Cloths,” “Coats and Cloaks,” “Hospital Sheeting,” “Knapsacks,” and “Tents.”36 A much shorter advertisement on the same page of the same edition of the newspaper focused on the company’s rubber shoes and carriage cloths, while mentioning that rubber clothing of every description was also available.
Warren may not have achieved officer status in the Newark India Rubber Company at the time of these three advertisements. However, he clearly had become one of the company’s officers at a time when Ricord suggests that the company nearly went under in 1850. At this time, “in opposition to [Warren’s] advice and that of others, an inferior article of rubber was purchased and manufactured into goods which proved worthless.”37 I have not been able (yet) to determine what caused the problem. However Woshner suggests that even after Goodyear’s successful attempts at applying sulfur and heat to rubber, and the patent based on this, some manufacturers had trouble using the process successfully in their own facilities. Consequently, there were poorly manufactured items still being produced. So, it could have just been growing pains for the Newark India Rubber Company.
Ricord goes on to explain that Warren went on from this near failure and “secured enough of the capital stock of the company to give him the entire control of its management, and its manufactured goods thenceforth bore a reputation for uniform excellence.”38 It was shortly after Warren had achieved control of the Newark India Rubber Company that Goodyear and the companies represented with him in “The Great India Rubber Case,” described above, were successful in their patent claims against Horace Day.
In 1853, Hiram Hutchinson, long-time president of the Newark India Rubber Company, left to found a new company in France. This may have been related to or impelled by Warren’s successful efforts to acquire a controlling amount of the company stock, possibly forcing Hiram out. Hiram’s new company, called Hutchinson, still exists today. Its company history indicates that Hiram Hutchinson started by manufacturing rubber shoes.39
In 1863, the following item appeared in a Sacramento newspaper, crediting Hiram and other Americans with making the company a huge success, making me think that even if Warren had forced Hiram out at the time of those “inferior goods,” it was not really for lack of expertise possessed by Hiram.
AMERICAN MECHANICS IN FRANCE.—There is at Montargis, in France, about three hours ride by rail from Paris, a grand India rubber company, operated by steam, and employing between 600 to 700 work people. The establishment was built by the father of Louis Phillippe, and with the dwellings of those employed in it is said to resemble a sort of baronial estate. The factory is managed by Mr. Hiram Hutchinson, formerly a citizen of Newark, N.J., and President of the Newark India Rubber Company, while the two chief foremen are also Americans (Canfield, of Connecticut, and Mix, formerly of the Newark India Rubber Company.) [sic] The establishment is owned by a corporation, who have a factory in Paris and another in Germany, and their enterprise has not only made them enormously rich, but been of very great advantage to France. The fact that three American mechanics hold the chief places in the employment of this great French firm at Montargis speaks eloquently in favor of the superior mechanical skill of our countrymen.40
Back in America, as the war progressed, there was a cutthroat rush to meet the demand for rubber blankets and other items for the Union army.
…the demand thereby occasioned for blankets, ponchos, rubber overcoats, haversacks, tents, etc., was so great, that the inducement to Companies, which were already in possession of the requisite machinery, to manufacture such articles, was strong … The Union Rubber Co. ,,, had the exclusive right to use his [Goodyear’s] process in the manufacture of Clothing. Some manufacturers attempted to ignore this fact, and proceeded to contract with the Government to furnish supplies of the articles named. Apparently successful in evading the many legal decisions which had established the validity of the Goodyear Patent, and the consequent right of Mr. Goodyear to dispose of it as seemed most proper, it was not until payment was expected on account of the contracts that the infringing parties found that there was a serious obstacle in their path. The Union Rubber Company had quietly stopped all payments on such contracts, unless the parties furnishing such supplies could produce a written permit or order from them. The only course that remained was to attempt some compromise upon terms not unreasonable, in view of the circumstances.41
Warren Ackerman was able to contract, sometimes directly, sometimes as a subcontractor, to provide various kinds of rubber goods to the Union Army. Woshner shows that chief among these goods were orders to provide rubber blankets, both through the Newark India Rubber Company and a company founded under his own name, Warren Ackerman and Company.
NEXT MONTH
Next month, I will introduce Ella King Adams, the person Warren turned to as he began to renovate his bargain purchase, the notorious Deserted Village, into a fashionable and secluded resort.
Until next month!
1 Ricord, F. W. History of Union County New Jersey, East Jersey History Company, Newark, N.J., 1897, p. 625. Hereinafter Ricord.
2 American Battlefield Trust, Civil War Casualties. November 16, 2012; updated September 15, 2023. Accessed online on April 22, 2024 at https://www.battlefields.org/learn/articles/civil-war-casualties#:~:text=Approximately%20one%20in%20four%20soldiers%20that%20went%20to%20war%20never%20returned%20home. Hereinafter Trust.
3 Dorwart, Dr. Bonnie Brice. “Disease in the Civil War,” online at https://www.essentialcivilwarcurriculum.com/disease-in-the-civil-war.html. Taken from Dr. Dorwart’s book, Death is in the Breeze: Disease during the American Civil War. Frederick, Maryland: National Museum of Civil War Medicine Press, 2009). Hereinafter Dorwart.
4 Trust.
5 Trust.
6 Donald, David Herbert, Editor. Gone For a Soldier: The Civil War Memoirs of Private Alfred Bellard. Little, Brown and Company, 1975. pp. 119-120. Hereinafter Bellard.
7 From Woshner, citing to National Archives, RG 92, Entry 225, Consolidated Correspondence File, “India-Rubber.”
8 Babits, Lawrence E. “Rubber Poncho and Blankets from the Union Transport Maple Leaf,” originally published in the Journal of the Company of Military Historians, Vol. XLVII, No. 2. Online at https://www.libertyrifles.org/research/uniforms-equipment/rubber-blankets. Hereinafter Babits.
9 Babits.
10 Babits.
11 Babits; also McGowan, Lauren, “Gum Blanket,” October 20, 2013. Emancipation Project website, online at https://udemancipationproject.wordpress.com/resources/objects/gum-blanket/. The Emancipation Project was a collaborative effort managed by project director Dr. J. Ritchie Garrison, Professor of History and Director of the Winterthur Program in Material Culture at the University of Delaware. Hereinafter McGowan.
12 McGowan.
13 Gaede, Frederick C. Ponchos and Waterproof Blankets During the Civil War. Military Images, March 2, 2022. Online at https://www.militaryimagesmagazine-digital.com/2022/03/02/ponchos-and-waterproof-blankets-during-the-civil-war/. Hereinafter Gaede.
14 Gaede.
15 Gaede.
16 McGowan.
17 Babits, quoting from Wilbur F. Hinman, Corporal Si Kelgg and his Pard (Cleveland: National Tribune, 1895) pp. 50-51.
18 McGowan.
19Advertisements placed in the Philadelphia Inquirer, Monday, October 27, 1862, p. 5.
20 Bellard, pp. 167-168.
21McGowan.
22 McCarthy, Carlton. Detailed Minutiae of Soldier Life in the Army of Northern Virginia, 1861-1865, Riverside Press, Cambridge, 1882. Pp. 76-77. Hereinafter McCarthy.
23 Woshner, p. 18.
24 Korman, Richard. The Goodyear Story, Encounter Books, San Francisco, 2002. Pp. 24-25. Hereinafter Korman.
25 Korman, p. 27.
26 Slack, Charles. Noble Obsession: Charles Goodyear, Thomas Hancock, ad the Race to Unlock the Greatest Industiral Secret of the Nineteenth Century, New York 2002. Pp. 27-28. Hereinafter Slack.
27 Babits, p. 2.
28 Babits p. 3
29 The facts set out here come from a recitation of facts in Decision in the Great India Rubber Case of Charles Goodyear vs. Horace H. Day, Delivered September 28th, 1852. New-York, 1852.
30 Korman, p.77.
31 Korman, p. 106.
32 Korman, p. 120.
33 Ricord, p. 625.
34 Advertisement in New York Tribune, Friday, January 1, 1847, p. 3.
35 Advertisement in The Evening Post, Tuesday, November 28, 1848.
36 Advertisement in The Evening Post, Wednesday, August 29, 1849, p. 3.
37 Ricord, p. 623.
38 Ricord, p. 625.
39 Hutchinson Corporate Website, Our History: “Reinventing Ourselves for Over 160 Years,” online at HISTORY | Hutchinson.
40Author unidentified, “American Mechanics in France,” The Sacramento Bee, Wednesday, September 9, 1863, p. 2.
41 J.L. Bishop, A History of American Manufacturers from 1608 to 1860, (Philadelphia, originally 1868), as quoted in Babits, p. 4.